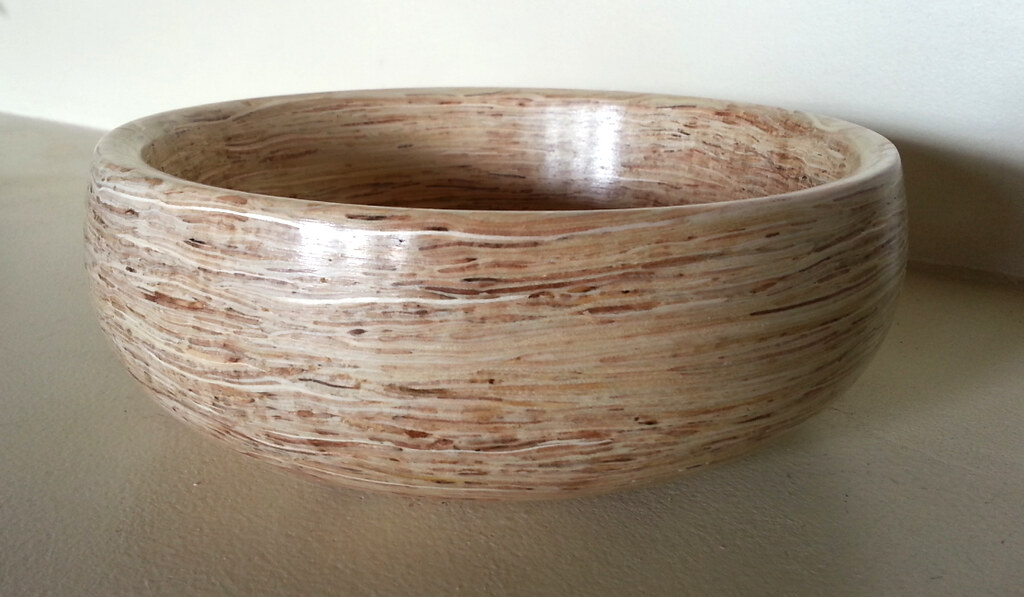
You may be looking for the best carbide tips to replace your drill's. We'll be discussing the cost of carbide tips and how reliable carbide teeth are. Learn how to maintain a sharp edge on your carbide tooth. You'll find the answers to all these questions and more in this article. We hope that this article has been helpful.
Materials to replace carbide
There are many advantages to resurfacing steel parts with a metal that is very similar to carbide. Firstly, the material's hardness will be increased due to its higher cobalt content. This combination is good as it will increase the toughness of a piece. If you care about toughness, it might be worth considering a more durable material. A carbide blade may not be sufficient. However, an alloy might be a cheaper option.
One advantage to using carbon-based materials is their ease of machine. Carbide may also be very fine which can make it difficult to machine. This can result in a smoother, more polished surface. The downside to this carbide type is its high manufacturing and processing costs. This material is a cost-effective option that can be used to cut intricate shapes. However, it is not as strong as other metals, and may break more easily.
Carbide cost tips
If you have a collection of woodturning tools, you probably have heard about the cost of carbide tips. They are more expensive than high-speed steel tools but they produce better results and catch more woodturning tools. But, they aren't cheap. You can expect to spend between $15-30 for a replacement carbide tip. If you use carbide tools only occasionally, however, you can be okay with the cost. Also, you can sharpen carbide instruments with a Diamond Stone, which is less expensive than sharpening tools.
You can use an old file to remove the old carbide tooth. But, if you're not comfortable doing it yourself, you can always use a ceramic rod. A flame will melt off the old carbide tooth, but it won't fall off on its own. Also, you can see how to retipe an sawblade. After you have removed the carbide tooth, it is time to install a fresh one. It should be the braze-alloy side of your new carbide tips.
Carbide teeth have a high degree of reliability
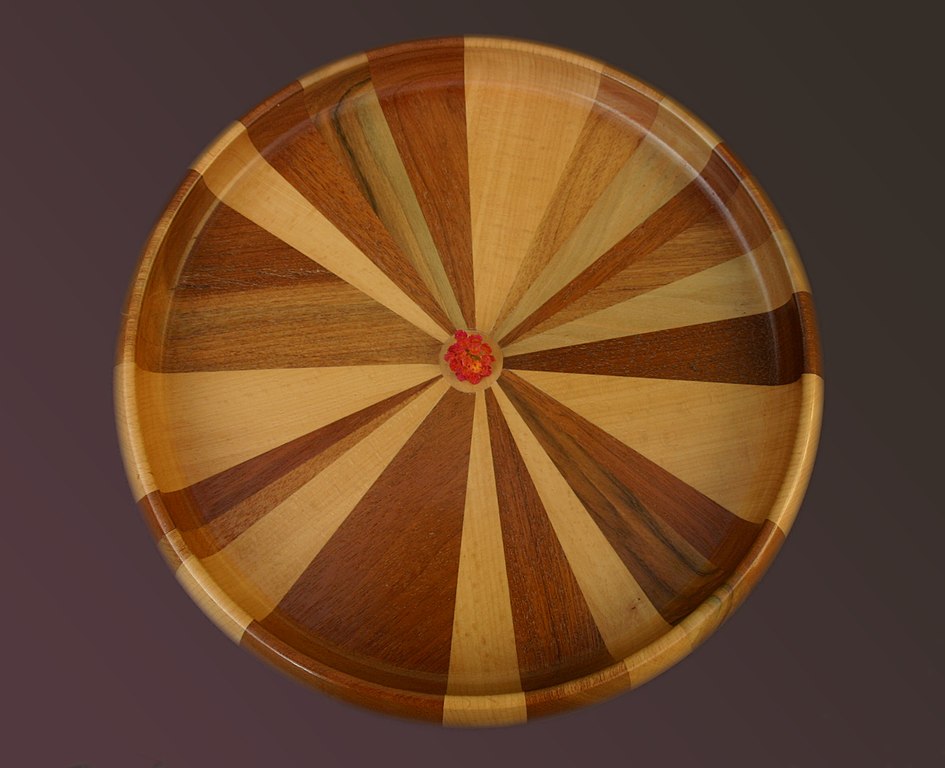
Unlike other replacement teeth, replacement carbide cutting tips are made with chrome-moly alloy steel and are dependable. These carbide-cutting teeth can be used with MacKissic-style stump chopping tools. They also have thicker carbide than originals, which prolongs their life span and increases their sharpening cycles. Here are some tips on how to install replacement carbide teeth. Follow these steps.
Getting a good edge on a carbide tip
Carbide cutting edges can last up to 25 to 100x longer than traditional high speed steel. If you need to sharpen your carbide tool again, you don't have to. High-quality carbide tools can be sharp enough to be used for woodturning, and razor-sharp enough to be used for hand plane irons. Here are some tips to help you get a sharp edge on a replacement caride tip.
Begin by placing the replacement carbide tips on a fine-grained diamond stone. Place your finger on the base and lightly press down. You want to evenly apply pressure on the front and back sides of the carbide tip. To create a square radius, make about 50 back-and forth passes. Next, rotate the tip 90° and repeat. Once you have created square radii, rotate the tip 90 degrees and repeat 10 times clockwise or counterclockwise.
FAQ
Do you have any other information I should know about woodworking and/or the process of making it?
It is easy to underestimate the amount work involved with furniture construction. Finding the right wood for the project is the hardest part. There are so many options for wood, it can be difficult choosing the right one.
Another problem is that not all wood has uniform properties. Woods can warp, split, or crack over time. Before purchasing wood, you should consider these factors.
What's the difference?
Hobbyists like making things with wood. Professionals focus more on quality. Hobbyists are proud of their creations and will often share them with family members and friends. Before they start working on a project, professionals will spend hours researching the designs. Professionals will be meticulous about all aspects of their work, from selecting the right materials to finishing it.
Do you have any suggestions for starting a woodworking shop?
It is hard work to start a woodworking company. However, if you are passionate about your hobby you will be willing to put in the effort. You will probably love the challenge of starting your own business.
Remember that you may encounter unexpected problems when starting a new venture. You may run out of money suddenly. Maybe customers won't be willing to pay what you want. You must be ready to deal with such situations in order to survive.
One tip is to have a separate banking account for your company. You'll be able to track how much money comes in and out.
How do you calculate woodworking costs?
Remember to keep costs as low as you can when calculating project costs. It is important to ensure that you are getting the best materials prices. Also, consider all other factors that can affect the price of your projects such as skill level, experience, time and cost. If you want to get an idea of what you can expect to spend on different types of woodwork projects, check out our guide to the average price of common household DIY tasks.
Statistics
- The U.S. Bureau of Labor Statistics (BLS) estimates that the number of jobs for woodworkers will decline by 4% between 2019 and 2029. (indeed.com)
- If your lumber isn't as dry as you would like when you purchase it (over 22% in Glen Huey's opinion…probably over 10-15% in my opinion), then it's a good idea to let it acclimate to your workshop for a couple of weeks. (woodandshop.com)
- Most woodworkers agree that lumber moisture needs to be under 10% for building furniture. (woodandshop.com)
- In 2014, there were just over 237,000 jobs for all woodworkers, with other wood product manufacturing employing 23 percent; wood kitchen cabinets and countertop manufacturing employing 21 percent. (theartcareerproject.com)
External Links
How To
How to stain wood
The process of staining wood involves the application of chemicals to the wood's surface, which causes it to change its color. The wood will turn from white to brownish-red due to the chemical reaction. The most common type of wood used for staining is oak, although many other types of wood can be stained.
There are many options for applying stains to wood surfaces. Some methods include mixing the stain along with a solvent like turpentine and then applying the mixture to the wood by brushing or spraying. Another method involves applying a solution of water to the wood. You can also mix stains with varnishes or paints so that they become part the finish coating.
Preparing the surface for staining wood is the first step. Clean the wood to get rid of any grease, dirt or other substances that might be detrimental to the stain's application. Sanding can smoothen out scratches and uneven spots. You must then decide on the type of stain that you wish to use. Penetrating stains are different from non-penetrating. Penetrating stain penetrates deeper into wood than nonpenetrating, making them suitable for dark colors like mahogany. Non-penetrating oils work best when used with light colors, like maple.
Once you have decided on the stain type that you want, get your tools ready. Because you can spread the stain evenly with a paintbrush, it is ideal for applying them. To remove any stains left behind after painting, you will need some rags. If you are planning to mix your stain, ensure you have enough containers for each component.
After you have prepared your materials for staining, clean the area. To remove dirt and dust, use warm water and soap. Wipe the entire piece of furniture with a rag dampened with clean water. Make sure you eliminate any loose debris, especially if you plan to stain darker wood.
Apply the stain next. Next, apply the stain to the furniture by starting at one end. Slowly and carefully move along the grain of wood, slowly but steadily, until you reach the other end. The stain should not drip off of the wood's edge. Before proceeding to the next step, let the stain dry thoroughly.
Apply a clear polyurethane sealant to protect the painted surface. Three coats are recommended for polyurethane. Let the third coat dry overnight before you sand the final coat.