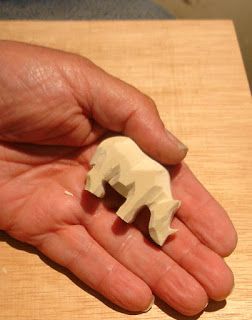
When you're looking for an oar carving knife, there are a few different things to keep in mind. When buying a knife, you should consider the following: size, sharpness, stagbone, lamination, origins, and so on. Learn how to choose the best one for you. The information in this article will help you to understand what to look for when shopping for an oar-carving knife.
Size
Oar Carver series is a collection of carving pocket knife that are a timeless and iconic example of this craft. Three sizes are offered in the current lineup. Version 2 is bigger and has a thinner blade. Version 3 comes in a slightly larger size with a thicker knife and a wider space between them. Here are some tips on choosing the right size.
Sharpness
A sharp edge is an important aspect of any oar carving knife. The edge of any oar carving knife will eventually show wear such as dullness, chips and nicks. It is important to keep your knife sharp. It is fairly easy to assess the sharpness an oar carver knife by simply observing its edge. A magic marker is able to match the knife's edge with the blade's center.
You can test the sharpness by cutting a piece from basswood across its ends grain to determine if it is. A blade should be perfectly sharp when it cuts through the wood without leaving ripples or drag marks. Smooth cutting is like slicing a baby's bum without leaving any marks. These marks indicate that the blade is not sharp enough to carve. Regularly check the sharpness and quality of your oar carving knife.
Laminated blades
The Oar Carver series, designed by world-renowned carver Ross Oar, has become a classic example of the carving pocket knife. There are currently three versions, Versions 1 and 2. Each version has a unique design. Version 2, for instance, has a larger difference between the blades. It also has a shorter edge. You can find more information in the Oar Carver blade guide.

Mora makes two versions of the 106 and 120. Both models are made with a laminated steel blade, but the Mora knife is longer. Both knives come with a simple oval handle and a snap sheath. The Mora Frost 122 is another model with a laminated carbon steel blade and a 61 Rockwell hardness. This knife is ideal for carving. It is very sharp and durable.
Origins
The oar carving knife was developed from ancient times in Japan. The handle measures four and a quarter inches in length and is made from solid hardwood. The oar features a long flat blade with a flat tip. The knife's shaft is 53 inches in long. The handle is made from a narrow, slender circle. The shaft and blade are separated by a thin slice of wood.
The earliest known carving tool is the oar, but its history runs much deeper. The oar was originally designed to be used by riverine and coastal people. Because it was easy to recognize and widely used, Admiralty chose the emblem oar. The oar might have had other meanings, however. Below are some examples of its origins. These are great if you're interested in the history of knife-making.
FAQ
How can I tell what kind of wood I am working with?
When purchasing wood, always check the label. The label should detail the wood species, its moisture content and whether it has been treated or not.
Are you looking for tips to start a woodworking company?
It can be difficult to start a woodworking shop. It's worth it if you're passionate and willing to work hard. You'll enjoy the challenge and rewards of owning your own business.
Remember that you may encounter unexpected problems when starting a new venture. For instance, you might run out of money unexpectedly. Or maybe you'll find that customers aren't willing to pay as much as you'd hoped. To survive, you'll need to be prepared for such situations.
Set up a separate account in your bank for your business. You'll be able to track how much money comes in and out.
Are you a genius in order to master woodworking?
No. Woodworking is not rocket science. Anyone can learn how to use basic power tools and techniques to create beautiful works of art.
What kind wood should I use for my project?
Woodworking is a popular job that involves oak, pine and maple. Each wood type has its own characteristics which affect the final product's appearance and feel. Oak, for example, tends be darker and more hard than other woods. Birch is lightweight and soft while mahogany is heavier and denser. You can also pick between veneers and solid wood. Veneers are thin wood sheets that are glued together to form one layer.
What is the difference between a hobbyist or a professional woodworker, and how can you tell?
Hobbyists like making things with wood. Professionals focus more on quality. Hobbyists usually take pride in their creations and often share them with friends and family. Professionals will spend hours researching designs before they begin working on a project. They'll be meticulous about every aspect of their work, from choosing the best materials to finishing it perfectly.
Statistics
- Woodworkers on the lower end of that spectrum, the bottom 10% to be exact, make roughly $24,000 a year, while the top 10% makes $108,000. (zippia.com)
- In 2014, there were just over 237,000 jobs for all woodworkers, with other wood product manufacturing employing 23 percent; wood kitchen cabinets and countertop manufacturing employing 21 percent. (theartcareerproject.com)
- Most woodworkers agree that lumber moisture needs to be under 10% for building furniture. (woodandshop.com)
- Overall employment of woodworkers is projected to grow 8 percent from 2020 to 2030, about as fast as the average for all occupations. (bls.gov)
External Links
How To
How to join two pieces of wood together without nails
Many people love woodworking. Woodworking can be a fun hobby because you can work with your hands to make useful objects from wood. However, there are times when you want to join two pieces of wood together without having to use nails. This article will explain how to do this so that your woodwork projects stay beautiful.
First, remove any sharp edges from the wood pieces before you join them. You don't want any sharp corners to cause problems later. Now you can start gluing the boards together.
If you are working with hardwood, only one side should be glue. For softwoods like cedar and pine, glue should be applied to both sides. Once the glue has dried, press the boards together until they are fully adhered. Be sure to let the glue dry before you move on to the next step.
After you glue your boards together, drill holes at the joints where screws will be inserted. Depending on the type of screw that you use, the size of these holes will vary. For example, if your screw is a 1/2-inch wooden screw, drill a hole that is at minimum 3/4 inches deep.
After drilling your holes, drive the screws into the board's backside. You should be careful not to touch the board's front surface. This could cause damage. Don't drive the screws too far into the end. This will prevent splitting in the end grain of the wood.
Once your project is complete, it's time to protect it against the elements. You can seal the furniture pieces or cover the top. It doesn't matter what method you use, you want something that will last many years. You can choose from oil-based varnishes or polyurethane, shellac and lacquer as examples.
These products can usually be found at any home improvement store. Be sure to choose the right one for your project. Some finishes are toxic and should not ever be used indoors. So, always wear protective gear when handling them.