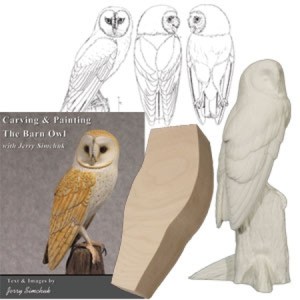
Chip carving can be difficult if you've ever tried it. There are many styles and techniques you can use, but which one is the best? What tools will you need? This article will give you my top tips and tricks when carving chips. You'll discover that chip carving success is possible with several key elements.
Traditional
Chip carving is one of the oldest forms of decorative woodcarving. You will need a straight-edged blade knife, but you can also use a skew-ground and offset knife. Chip carving involves making numerous small triangular holes in the wood to create a pattern. This art form was developed simultaneously in several countries and dates back over 1000 years. It was so popular that many designs looked the same across nations, making it difficult to tell which one was which.
As the practice spread throughout the world, the skills required to carve wood were passed down from generation to generation. Chip carving was used in Sweden to decorate furniture. Schools were eventually established to teach this art. Modern chip carvers are able to benefit from the centuries-old skills and knowledge of carvers. Through the generations, knowledge and experience was passed down from carver to apprentice and student. It's a continuous process that continues into the present.
Formulary free
This DVD will teach you how to chip carve. Murray Taylor gives you a DVD on how to create geometric and freeform carvings. It is an excellent introductory project with plenty of information. English and NTSC formats are also available. You can also purchase the DVD in stereo and widescreen. Artisan Media Ltd. holds the DVD. It can also be downloaded in MP4 format to Windows and Mac computers.
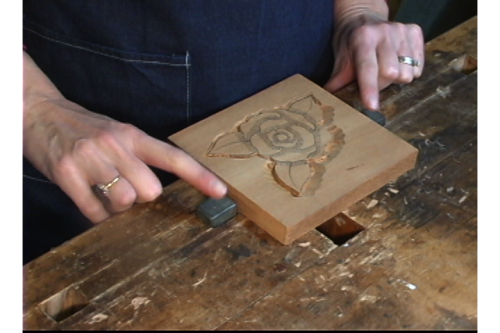
The basic shapes in geometric chip carving are triangles, circles, and lines. This technique allows for endless shapes and patterns, and can also be used to combine various styles. This technique is also known by the free-form style of chip carving. You can make your chips look beautiful in any room, no matter whether they are a flower, a dragon or a tree. A free-form method of chip carving is a great way to incorporate several different techniques into one piece.
Techniques
Chip carving has been around for centuries. There are many examples all over the world. In the South Pacific Islands, for example, chip carving has been found on boat paddles and ceremonial tool handles. Although most of these carvings were done with bits of bone or seashells, some have also reported using shark teeth. This book demonstrates how to use a variety of chip carving techniques to produce stunning designs.
If you are able to follow some simple steps, chip carving can be easy. The first step is to learn how you can carve the fine triangle. This pattern is very easy to comprehend and execute. To carve this design, simply carve different triangles and do it again. However, chip carving doesn't have be boring. Variation of the triangles can give you a wide variety of patterns.
Tools
Lora S. Irish offers a free online seminar that will teach you the basics of chip carving. She will teach you how use different carving tools and supplies such as a chip and stab knives, detail bench knife, and detail table knife. Irish will also cover the various types of wood carving tools in this free seminar. To purchase the right tool, you can choose from this list. You can use these tools to create simple shapes and designs, or work more intricately and make more intricate designs.
Special geometry is used to create a chip carving knife. It is one-half inch in length and has an angled back edge. This makes it easy to make precise cuts. It is also important to choose a sharp, needle-sharp point so that the edges meet perfectly. Chip carving knives are also made of stainless steel and come with a sharp tip. A chip-carving knife should be sharp enough for cutting a small piece of wood.
Getting started
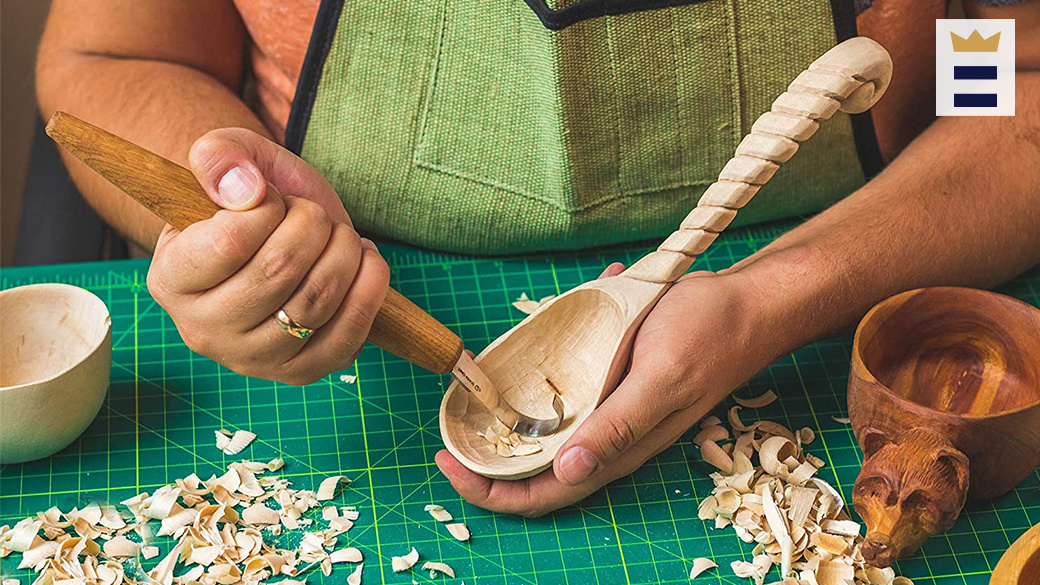
When getting started with chip carving, you must first learn about its methodology. This process varies based on the type of carving that you intend to do. Nevertheless, you should be aware of some basic principles to ensure that your work is as accurate as possible. Chip carving is a technique that involves creating a fine pattern in wood. To create your first chip carving, follow these steps:
It is vital to sharpen your chip carving knife properly. A chip carving knife's blade will have bevels at each end. This indicates that it is primary. The sharpening tool is shaped like a small diamond and can produce sharp edges. Place it at a ten degree angle. The stone will sharpen the chip carving knife and chip carving tool at the same time.
FAQ
Is it possible to open my own woodworking shop?
It's not easy to start your own woodworking business. You will need to adhere to many legal requirements. This doesn't necessarily mean that you should go through all the work of setting up a company. Many people opt to join existing businesses instead. You only need to pay membership and tax fees.
How do I choose the right tools for me?
When shopping for tools, it helps to think about your needs and preferences. What do you prefer: metal or plastic handles? What size of nails and screws do your hands use most? Would you rather use hand tools than power tools?
Do you have any tips on starting a woodworking business?
It's not easy to start your own woodworking business. But if you're passionate about your hobby, you won't mind putting in the effort. You'll likely enjoy the challenge of owning your business.
It is important to remember that unexpected problems may arise when you start a new venture. You might run out money, or you may have to borrow unexpectedly. Maybe customers won't be willing to pay what you want. These situations are necessary for survival.
One good tip is to set up a separate bank account specifically for your business. You'll be able to track how much money comes in and out.
What kinds of woods are good for making furniture?
Woods are classified according to their hardness. Softwoods include cedar, pine, cedar, and Cypress. Because they resist rot, softwoods can be used to make outdoor furniture. The hardwoods are oak, maple and mahogany. Because they can't weather outside, they're usually used indoors.
Statistics
- In 2014, there were just over 237,000 jobs for all woodworkers, with other wood product manufacturing employing 23 percent; wood kitchen cabinets and countertop manufacturing employing 21 percent. (theartcareerproject.com)
- The U.S. Bureau of Labor Statistics (BLS) estimates that the number of jobs for woodworkers will decline by 4% between 2019 and 2029. (indeed.com)
- Average lumber prices rose about 600 percent between April 2020 and May 2021. (familyhandyman.com)
- Most woodworkers agree that lumber moisture needs to be under 10% for building furniture. (woodandshop.com)
External Links
How To
How to stain wood
Staining wood is the process of applying chemicals to the wood's exterior, which alters its color. The wood will turn from white to brownish-red due to the chemical reaction. Oak is the most common wood type for staining. However, you can also use other wood types.
There are many ways to stain wood surfaces. One method involves mixing the stain and a solvent and then spraying it on the wood. Others use a solution made up of water and dye, which is then applied directly onto the wood. You can mix stains into varnishes or paints to make them part of your finish coat.
The first step in staining wood is preparing the surface. The wood must be thoroughly cleaned to remove all grease and dirt. Sanding can smoothen out scratches and uneven spots. The next step is to choose the stain type you want. There are two main kinds of stains available: non-penetrating stains and penetrating. Penetrating stain penetrates deeper into wood than nonpenetrating, making them suitable for dark colors like mahogany. Non-penetrating stains work best with light colors like maple.
After you've decided what type of stain to apply, get ready for your tools. The best tool for applying stains is a paintbrush. It allows you to evenly distribute the liquid over the surface. To remove any stains left behind after painting, you will need some rags. You should have enough containers to store the various components of the stain mixture if you intend to mix it yourself.
After you have prepared the materials, you can clean the area where you want to stain the wood. Use soap and warm water to remove dust and grime. Use a dampened sponge and warm water to clean the entire piece. Make sure you eliminate any loose debris, especially if you plan to stain darker wood.
Apply the stain. Start at one end of the piece of furniture and brush or spray the stain onto the wood. Move slowly and carefully along the grain of your wood until you reach its opposite end. The stain should not drip off of the wood's edge. Before moving on to the next steps, allow the stain drying completely.
A coat of clear polyurethane sealing agent is applied to protect the paint. Three coats of polyurethane sealing agent are required. Allow the third coat to dry overnight before sanding the final coat.