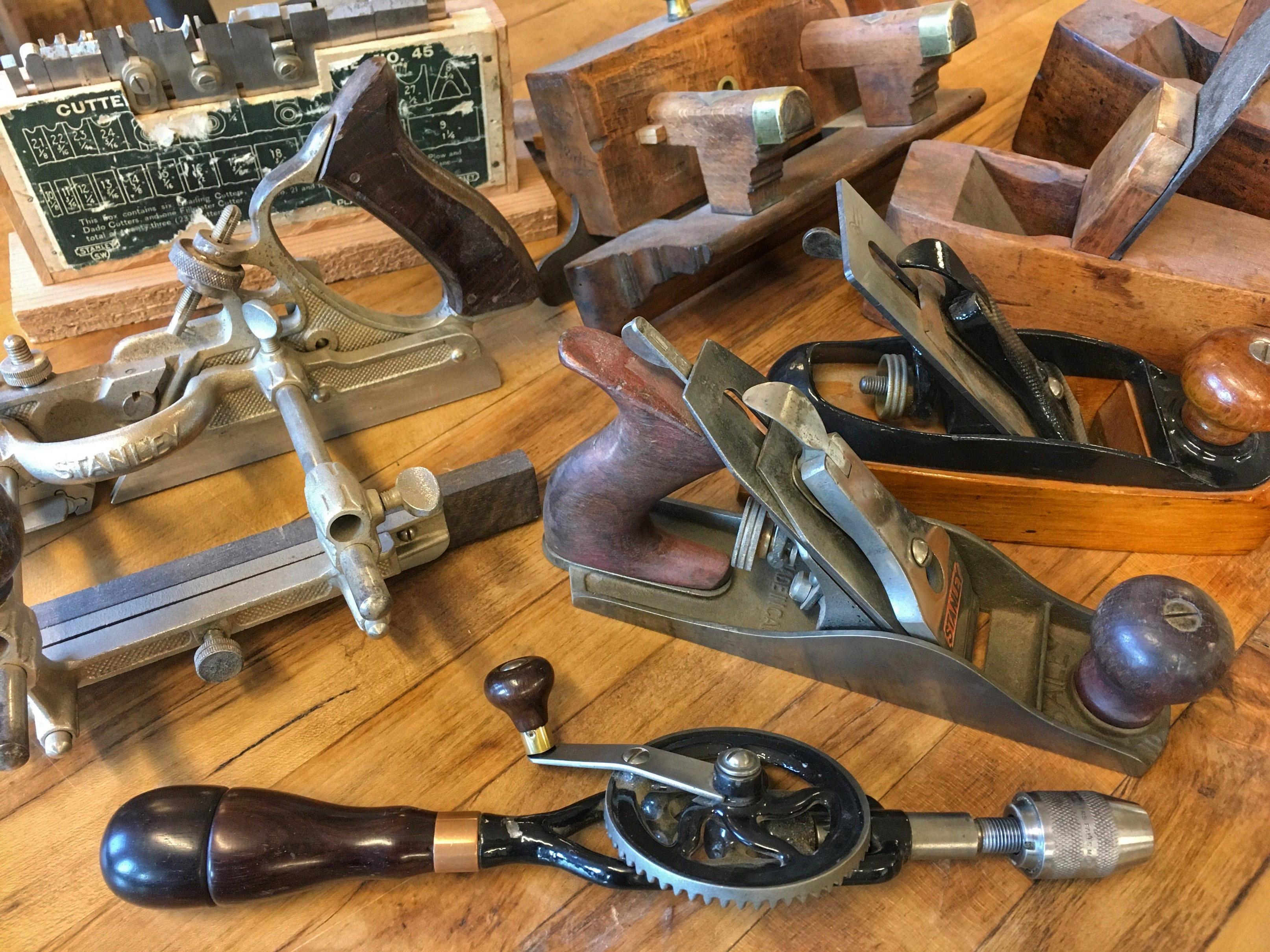
It can be difficult to transport rough lumber in your car. You should always bring your hand saw, tape measure and other tools with you to the store. Also, make sure to buy extra boards in the event that the one you have purchased doesn't fit. You should also ensure that the board has checks and knots. They may not be as easy to plane down as you expected. You don't want to have to rip a board and start all over. This will waste time and money, so it's best to buy one or two extra boards.
Minimal wastage
When cutting rough lumber, a sawmill typically turns 59% of the log volume into boards. The remainder of the log, which includes sawdust or bark, is considered waste. Although a less perfect cut can result in more waste than a perfect cut, it should still not exceed 20%. Here's a quick formula to determine how much wasted wood is in a particular board. The sawmill should reduce 18% of its volume in order to get the desired lumber thickness.
For one, rough lumber is rarely available in uniform dimensions. The dimensions of hardwood you buy from big box stores are usually known. This allows you to plan your project according to the standard size. Rough lumber's edges don't always match up perfectly, causing waste. Additionally, rough-cut lumber often requires a common width which results in a lot wasted lumber. These wastes can't be recycled later.
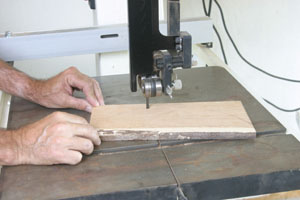
Preparation
Measure the length of your material before you start cutting rough lumber. Rough lumber may not arrive at the lumber yard perfectly flat. You may need to flatten it several times as it may not have parallel edges or faces. It is a good rule of thumb to take out 1/16" per pass. If the lumber has concave surfaces, run it through the saw with the concave surface down.
Rough cut lumber should be flattened to a thickness of 1/4 inch before it is cut. After flattening the surface, plane to the final thickness of the board. Once you have measured the rough lumber's thickness, measure the finished width & length. Be aware of any imperfections and plan accordingly. Always leave a margin of about one-quarter inch on both sides of the board, and plan your project around the available boards. Make sure the lumber you buy is flat enough, as rough boards that are warped, bowed, or twisted are difficult to work with.
Cost
There are two types. Dimensional lumber and rough-sawn. Home improvement stores generally carry finished lumber but very rarely rough-sawn. Both types of lumber are often available at local sawmills and lumber yards. The main difference is in how much work they need to be processed. Because it is less processed, rough-sawn boards can be more economical. It is also wider and thinner than finished lumber.
A lumber yard or mill will generally sell lumber at a lower price, but they are less likely to have standard lengths. While milling your lumber yourself can be cheaper than purchasing rough-sawn lumber at a lumber yard or mill, it will require more space and better power. It can also be noisy and requires some training. Zoning laws may be necessary if your mill is to be used in an area.
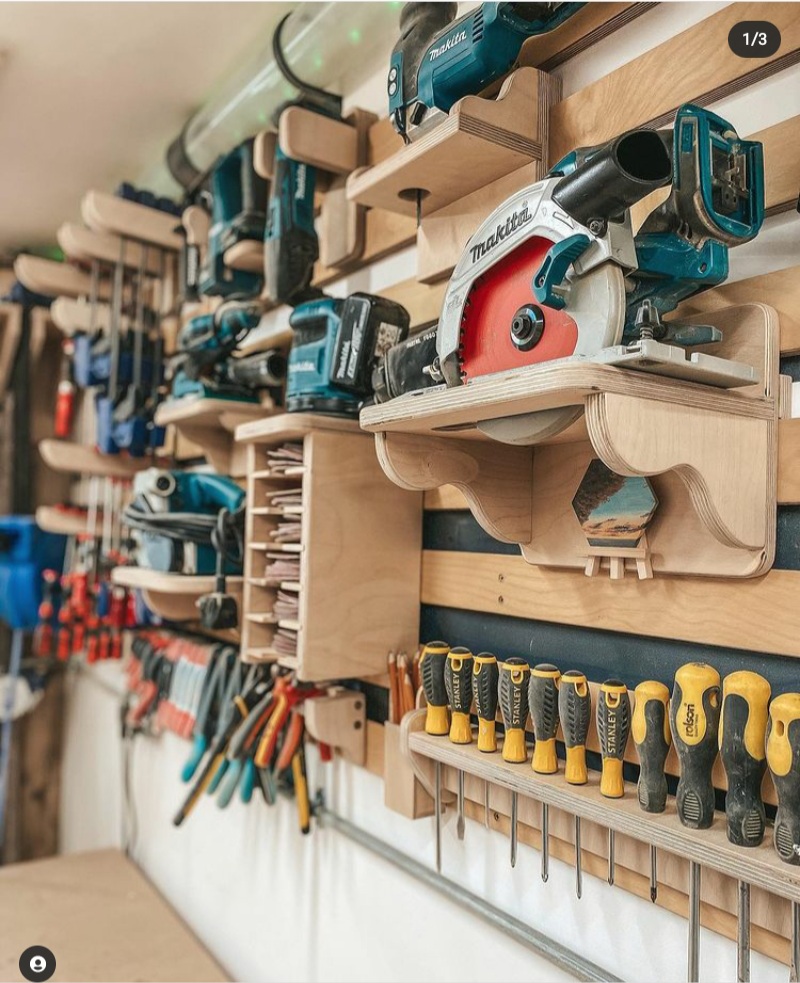
Source
When buying lumber, you have a number of options. There are many sizes, shapes and finishes available. Rough sawn lumber, by example, is unfinished lumber. It has been cut into boards. This lumber tends be more sturdy than other types, as it has more moisture. Additionally, it is thicker that surfaced wood. The following are some benefits of using rough sawn lumber for your woodworking projects.
The first is the availability and low cost. Rough lumber is not treated and is not usually sold at a hardware store. However, this type of lumber has its pros and cons. It's cheaper by volume but more expensive per board foot to haul. It takes longer to finish than treated wood. This is why you might consider it when deciding on how much lumber you want to purchase. You might consider buying a lot of rough sawn lumber to finish your project.
FAQ
How can I determine which tools are most suitable for me?
It's important to consider your preferences and needs when buying tools. Do you prefer metal or plastic handles? What size screws or nails do you prefer? Are you comfortable with power tools, or would you rather use hand tools?
What types of woods are best for furniture making?
Woods are classified according to their hardness. Softwoods include pine, fir, cedar, and cypress. Because they are resistant to rot, softwoods are often used as outdoor furniture. The hardwoods include teak, maple, mahogany and oak. Because they are not weather-resistant, they are best used indoors.
How can you calculate the woodworking price?
The most important thing to remember when calculating costs for any project is to keep them as low as possible. Always make sure you get the best price on materials. It is also important to consider the costs of other factors, such time, skill, and experience. Our guide to the average household DIY task price will give you an idea of how much it costs to complete different types of woodwork projects.
How can I tell what kind of wood I am working with?
Always verify the label on wood purchases. The label should provide information about the wood species, moisture content, and whether preservatives have been used.
Where do I start with woodworking?
The best way to learn how to build furniture is by building furniture. While you will need tools and make mistakes, you will eventually master the art of building furniture.
You should first choose the project you wish to complete. It can be something as simple and small as a box, or large-scale as an entertainment center. Once you've decided on a project, find a local woodworker who specializes in that kind of work. Ask the local woodworker for help in deciding what tools and where to get them. Ask if you can find someone who does this kind work.
How much money does a hobbyist have to put into getting started?
It is likely that you will need some capital in order to buy the required tools and supplies if your goal is to open your own woodworking business. The best place to start is by buying a small drill press, circularsaw, circular saw or sanding machine. These items aren’t too expensive so you won’t have to break the bank.
Statistics
- Overall employment of woodworkers is projected to grow 8 percent from 2020 to 2030, about as fast as the average for all occupations. (bls.gov)
- If your lumber isn't as dry as you would like when you purchase it (over 22% in Glen Huey's opinion…probably over 10-15% in my opinion), then it's a good idea to let it acclimate to your workshop for a couple of weeks. (woodandshop.com)
- The best-paid 10 percent make $76,000, while the lowest-paid 10 percent make $34,000. (zippia.com)
- Average lumber prices rose about 600 percent between April 2020 and May 2021. (familyhandyman.com)
External Links
How To
How to make wood joints
This tutorial will show you how to join two pieces of wood together. We will use the pocket hole joint, which is drilling holes in the wood to join them. This works well if the wood is straight and smooth. You may want to consider other methods, such as dowel joining. Here are the steps
-
Drill Pocket Hole Joints. Measure and mark the location where you would like to place the pocket hole joint. Then drill 3/4 inch deep holes into the ends of each piece of wood using a jig saw or handheld drilling machine.
-
Sand Smooth. Sanding the edges of the wood will help to prevent the joint from splitting later.
-
Glue together. Apply glue to both sides of the wood. Allow the wood to rest for five minutes before clamping it together.
-
Secure the pieces together. After the glue has dried completely, you can clamp the pieces together until they are flush.
-
Trim Joinery. Trimming the joinery after glue has completely dried.
To be able to turn the pieces inside-out, leave enough room between them.